|
Show content only (no menu, header)
To develop and validate the techniques required for the 1-m ultra light telescope, I have started to make a 0.6-m prototype primary mirror. The goal is to demonstrate that a sub-cm thick glass mirror of high optical quality can be manufactured and its shape can be maintained in a wide range of conditions (elevation, temperature, pressure).
The approach I am taking is to make a very stiff passive support (the backplate) on which the mirror will rest. The glass mirror is then soft-bonded to the backplate. The soft bond (a thin layer of silicone rubber) compensates for unavoidable mismatch in CTE, CME and to mitigate transfer of the mechanical deformations of the backplate to the optical surface. The goal of the backplate and soft bond is therefore to simulate a zero-gravity environment.
Carbon Fiber backplate
The CFRP backplate is composed of two CFRP plates on either side of CFRP beams. This offers a lightweight stiff composite plate.
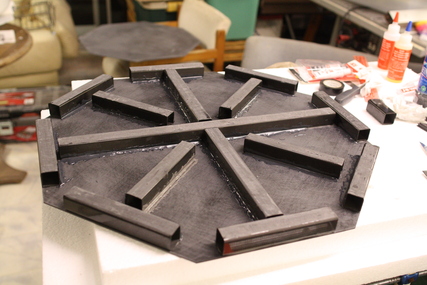 |
Carbon fiber backplate during assembly. The bottom plate and CFRP beams are visible in this image. The CFRP bottom plate is an hexagon (0.6-m between opposite sides).
|
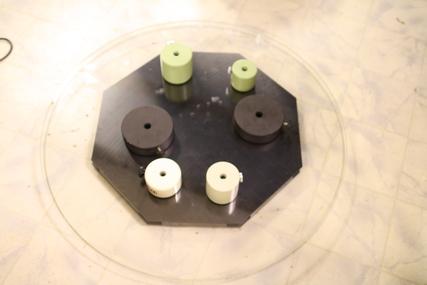 |
Carbon fiber backplate during assembly. Weights are used to press the 3 layers (bottom plate, beam, top plate) during epoxy curing.
|
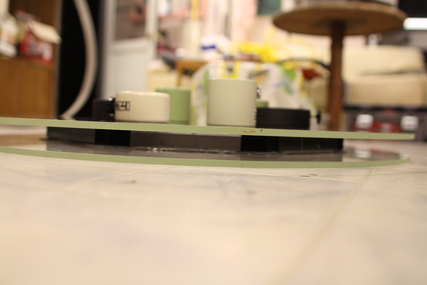 |
Carbon fiber backplate during epoxy curing. Side view. Large glass disks are used to ensure flatness and even load distribution.
|
Replication
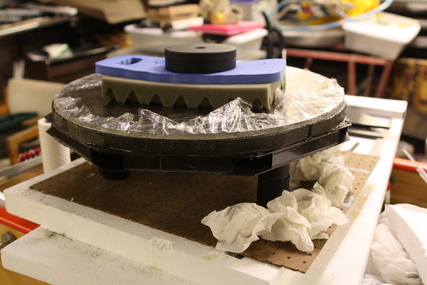 |
Replication: The CFRP backplate + machined foamglass is at the bottom of the stack. Epoxy has been spread on top of the foamglass. The glass mirror is pushed down, ensuring that the epoxy replicates its shape.
|
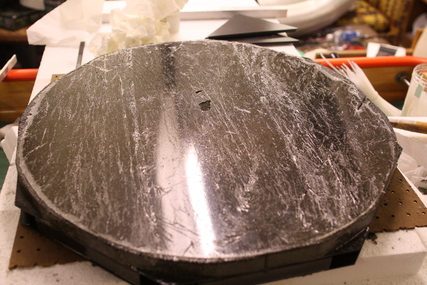 |
Replication: initial result, after removal of the mirror. The cured epoxy is smooth, and matches very well the shape of the glass mirror's bottom surface.
|
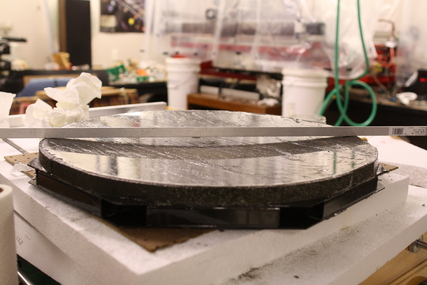 |
Replication: initial result. The quasi-parabolic shape of the replicated surface is visible here.
|
Page content last updated:
27/06/2023 06:35:52 HST html file generated 27/06/2023 06:34:42 HST
|