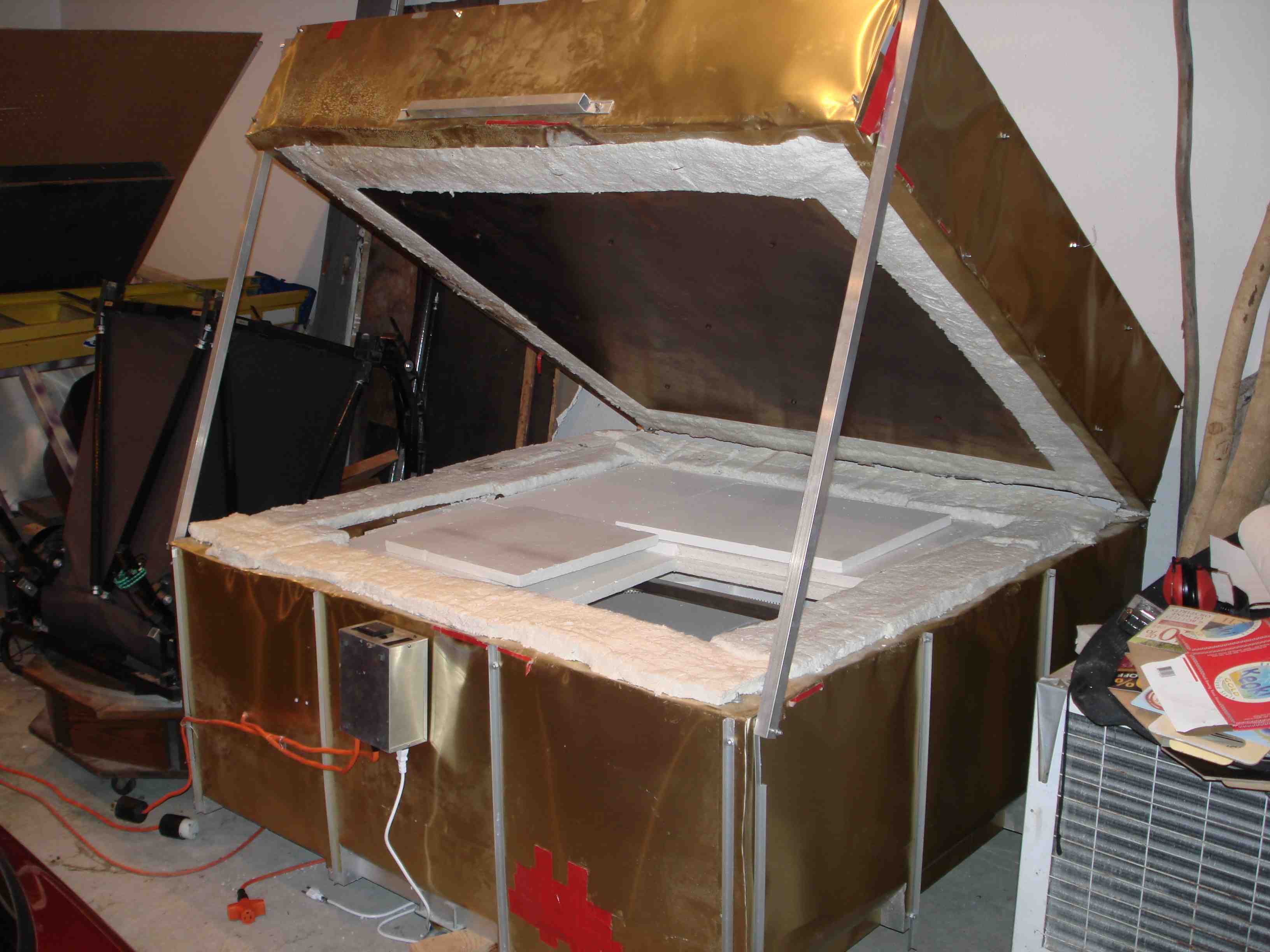 |
The oven is used for slumping glass over a mold, and can accomodate up to ~1.1m diameter blanks/molds. It is very lightweight (when empty !) and can be easily wheeled around in my garage. Several friends have suggested it would be best used to cook large pizzas/cakes/meat (a pig would fit in it!).
The picture on the left shows the oven with its lid open. The inner chamber is lined with high temperature insulation boards (white). In this picture, some of them are removed for partial access to the inside of the oven. In the picture below, the inner chamber is closed but the lid is still open.
|